How Risk Simulation, Uncertainty, and Randomness May Affect Building Product Manufacturers
- < Creating Space to Nurture Our Human Nature in the Built World
- > 3 Tips for Writing AIA Course Learning Objectives
How can building product manufacturers distinguish between luck and skill? How can product reps determine if their specification efforts got them specified on a large NFL football stadium or if it was simply chance and good luck? Being at the right place at the right time. We’ve all seen the lucky fool who benefitted from a disproportionate share of luck but attributed their success to their skillset. How can construction projects reduce risk and specify building products that have a lower risk to fail? These are big questions that we may not ever have a concrete answer for.
When Luck Is Mistaken for Skill
In his book Fooled By Randomness: The Hidden Role of Chance, author Nassim Nicholas Taleb discusses randomness disguised and perceived as non-randomness. Taleb examines the confusion between noise and signal in the marketplace. Some people read too much into things. Taleb’s main lesson throughout the book is that we underestimate the share of randomness in about everything.
Taleb doesn’t propose an all or nothing proposition. He states that the world is more random than we think, not that everything is random. A strong work ethic, persistence, patience, and an intellectual curiosity are all needed to be successful. But even building product reps that are very hard working can have a string of bad luck and not get their products specified. Why is that?
The fact that every smart, hardworking, persistent person becomes successful doesn’t imply that every successful person is necessarily smart, persistent, or hardworking. Taleb argues that one cannot judge a performance in any given field, say product specification, by the results, but by the costs of the alternative. What if history played out in a different way?
What if your concrete block was specified on three high schools after the bond passed instead of one high school? What if none of your exterior cladding was specified on the new Atlanta Children’s hospital and a no-name competitor won the bid? What if your product rep slept in late one Friday after imbibing three pitchers of Sangria at the company Christmas party and missed delivering an important AIA lunch and learn to a firm which cost you a job?
Taleb argues that humans are not wired to understand probability. Not everything can be summed up instantly “in a nutshell.” As Einstein once said, “common sense is nothing but a collection of misconceptions acquired by the age of eighteen.”
Monte Carlo methods or experiments are a class of computational algorithms that rely on repeated sampling to obtain numerical results. Monte Carlo simulations and experiments use randomness to solve problems that might be deterministic in principle. Monte Carlo simulation methods were used by the Los Alamos laboratory during the development of the A-bomb.
Currently, Monte Carlo methods are being used in multiple applications such as predicting the energy output of a wind farm during its lifetime giving different levels of uncertainty. Monte Carlo simulations are being used in reliability engineering to compute system-level response given the component-level response for transportation networks during an earthquake.
The white paper, Stochastic Risk Analysis and Cost Contingency Allocation Approach for Construction Projects Applying Monte Carlo Simulation was released in 2017. The researchers used Monte Carlo Simulation with the aim to determine the probability distribution of the contingency cost and the related level of risk coverage for construction projects. What are the impact of risks on a construction project using schedule, cost, and performance?
Monte Carlo Simulation is comprehensive, easy to use, and feasible for construction projects. Simulations can help prevent companies with cost overruns. The authors indicate that risk identification is one of the most important steps to recognize whole risks, which can affect the project budget. The risks may include operational, financial, or legal. The authors applied their method to a real world industrial project related to railway infrastructure.
The research team identified high, medium, or low impacts for scale. They noted that “it is necessary to take into account the fact that any risk can occur on a variety of values in terms of economic impact.” The research team concluded “the application for a real life company executed for two probability distributions, which presented the cost contingency amount to allocate in the project. The presented method is powerful as it can show the contingency amount for the risks happening with the determined probability (under 20 percent) and estimates the contingency value to cover all the possible risks.”
The bottom line: The risk management simulation for schedule, cost, and performance could identify key factors that caused delay in completion of certain activity, which if not attended may occur again and cause difficulties in completion of a project.
Avoiding Risk & Tragedy
On July 17, 1981, one of the deadliest structural collapses took place in the United States. 114 people were killed and 216 people were injured when walkways collapsed at the Hyatt Regency Kansas City Hotel. Approximately, 1600 people had gathered to participate in a dance. The fourth floor walkway collapsed onto the second floor walkway crushing people to death.
A flawed design change doubled the load on the connection between the fourth floor walkway support beams and the tie rods carrying the weight of the walkways. The design change was barely adequate to support the dead load weight of the structure itself, much less the added weight of the spectators.
To make matters worse, the hotel's sprinkler system had been severed by falling debris, flooding the lobby and putting trapped survivors at risk of drowning. As the pipes were connected to water tanks, not a public source, the flow could not be stopped. It’s a miracle no one drowned. During the rescue, one victim's right leg was trapped under an I-beam and had to be amputated by a surgeon, a task which was completed with a chainsaw.
An investigation uncovered details that could have prevented the loss of life. The drawings prepared by the structural engineer Jack D. Gillum and Associates were only preliminary sketches but were interpreted by Havens Steel Company as finalized drawings. Jack D. Gillum and Associates failed to review the initial design thoroughly, and accepted Havens Steel Company’s proposed plan without performing basic calculations that would have revealed its serious intrinsic flaws — in particular, the doubling of the load on the fourth-floor beams. It was later revealed that when Havens called Jack D. Gillum and Associates to propose the new design, the engineer they spoke with simply approved the changes over the phone, without viewing any sketches or performing calculations.
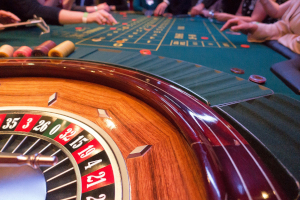
At least $140 million was awarded to victims and their families in both judgments and settlements in subsequent civil lawsuits. Life and health insurance companies are likely to have absorbed even larger uncompensated losses in policy payouts. The effect of a rare event can cause deaths in a building and bankrupt the companies involved.
Could Monte Carlo Simulation have helped prevent this rare event? If the project team was more diligent, provided more oversight, and ran multiple risk management simulations they may have discovered that the support beams and the tie rods carrying the weight of both walkways were insufficient. How can project teams minimize risk for rare events?
Architects Like to Specify Older, Proven Products
One strategy that architects use to avoid problems on a job is to specify a well-known product. Many building owners or partners of an AEC firm want a product that they know will perform and not cause problems; therefore, avoiding lawsuits and in rare cases deaths. They pay premiums and deductibles for the firm’s professional liability insurance, which can be very high and increase with each new lawsuit.
Performance characteristics also play a crucial role in specification and liability decisions. The architect doesn’t want to get sued when exterior cladding falls off the side of a fifty-story skyscraper and kills a family of four below. A product must meet certain building code requirements. Architects, specifiers, engineers, contractors, and other professionals will avoid a building product that may fail prematurely under normal use.
The more exposure your product has, the better chance it has getting specified. AIA online courses that educate architects about your products help build brand awareness and case studies prove their worth and value. In a previous blog, How to Get Specified by Architects—Part 2, we discussed how to influence specification through triggers and cues. Product manufacturers that develop products that solve problems for architects will form strong, positive associations with designers over time. It can take months or even years for architects to specify a product.
Book author Taleb argues that many people are fooled that new technologies and inventions revolutionize our lives for the better. We can only see the winners. Aside from major tragedies like the Hyatt Regency collapse, how many construction projects suffer from small product failures that when added together cost the country millions or even billions of dollars.
The AEC community prefers the “survival of the fittest”. If a proven product has been used for seventy years with low failure rates, the new competing product that dropped off the assembly line yesterday will probably have a difficult time getting specified. Older products have been exposed to rare random events and may be more resistant to risk. Risk averse architects will avoid brand new products with no proven track record.
Building Schedule Risk Analysis
In July 2015, The International Research Journal of Engineering and Technology released a study entitled Construction Building Schedule Risk Analysis Using Monte Carlo Simulation . The research team noted that “To organize and complete your projects in a timely, quality and
financially responsible manner, you need to schedule projects carefully. Effective project scheduling plays a crucial role in ensuring project success.”
The goal of the study was to identify key risk factors that affect project schedules, and to determine the probability of completing a project within due date. Project delays can increase the cost of the project and contractor may have to face penalty for causing delays. A risk management process which includes risks in execution that affects the project schedule is crucial.
Parameters that are associated with risk include: higher costs, extension of the project, failure to satisfy specified quality requirements, failure to satisfy specified information requirements, and failure to satisfy specified organizational requirements.
The researchers divided risk into two categories: dynamic risks and static risks. Dynamic risks are the risks where risk takers are concerned about making opportunities. It means there will be potential gains as well as losses. Dynamic risk is risking the loss of something certain for gain of something uncertain. Static risks are where people are concerned with potential losses and ways to minimize the losses. The unsystematic management of risks can affect the scope and success of the project since most risks are very dynamic throughout the project lifetime.
The research team used the construction of a hostel as its test subject. A team of experts were formed including both the contractor’s and owner’s site engineers and sub-contractor. The team was asked to grade identified risks in terms of probability and impact by grading them from 1 to 5. The probability impact matrix included three categories: low risk, medium risk, and high risk. Next a schedule risk analysis was performed using Monte Carlo simulation with @Risk software. The Monte Carlo Simulation calculated durations of the project based on the inputs.
For example, for the building foundation, the optimal time was 27 days, the most likely time was 28 days, the pessimistic time was 33 days, and the simulated time was 30 days. An output is defined, and beta simulation is run at, 10,000 iterations. After 10,000 trials, the mean completion time of the project was 292 days. The minimum completion time was for 288 days and the maximum completion time was 294 days. The results showed that it is extremely unlikely to complete the project within 282 days. This is critical information that affects the entire team.
Principles & Generic Guidelines on Risk Management
ISO 31000 is a family of standards related to risk management codified by the International Organization for Standardization. ISO 31000 provides a universally recognized paradigm for practitioners and companies employing risk management processes to replace the myriad of existing standards, methodologies and paradigms that differed between industries, subject matters and regions. AEC firms can use the ISO principles to approach risk. ISO 31000:2009 gives a list on how to deal with risk:
- Avoiding the risk by deciding not to start or continue with the activity that gives rise to the risk
- Accepting or increasing the risk in order to pursue an opportunity
- Removing the risk source
- Changing the likelihood
- Changing the consequences
- Sharing the risk with another party or parties (including contracts and risk financing)
- Retaining the risk by informed decision
Risk and Reasons for Failure
There are several reasons why a project may fail. Specification errors, omissions, and inaccurate prices for labor and materials are a few reasons. Project managers are tasked with preventing cost overruns and errors. Staying within budget can sometimes seem like a bad Monopoly game where you keep landing on Park Place and paying through the nose!
Delays can be a big problem as well. Permits delays and licenses can slow things down to a crawl. In addition, manufacturers can cause problems if their products don’t arrive on-site on time. If a product can’t meet a project deadline, then an alternate product might be selected. Local products are preferred but many times building products must be shipped across the country. Is a certified installer available in the area? These are all issues to contemplate.
Having great insurance in place is a must for AEC firms. However, natural disasters, structural issues, and rare events should be considered. Rare events can take all shapes and forms. The best project managers, risk managers, and consultants using Monte Carlo Simulation hopefully can better prepare for these rare events. However, the simulation is only as good as the information that is input into the simulation. Garbage inputs can lead to garbage outputs.
Ultimately, risk management software like Monte Carlo Simulators can help companies avoid pitfalls and discover opportunities. The quantitative analyses can help develop better strategies to minimize risk, identify factors that cause risk, and reduce costs. Predicting the future is impossible. But if Monte Carlo Simulation can reduce risk, it is worth considering. Has your company used Monte Carlo Simulation for risk management? How do you view uncertainty, risk, luck, and rare events in your daily work?
For more information or to discuss the topic of this blog, please contact Brad Blank